Embarking on an injection molding project? Selecting the appropriate injection molding machine tonnage is paramount for success. In this guide, we’ll navigate the intricacies of choosing the right injection molding tonnage for your project.
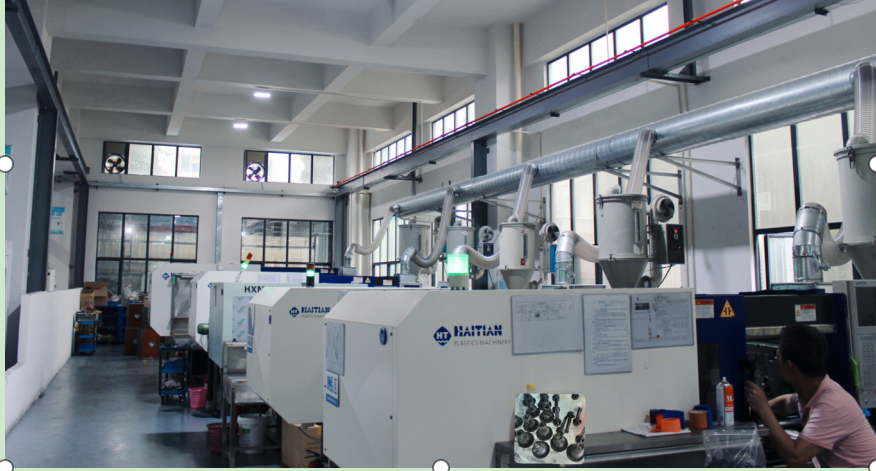
What’s injection molding tonnage?
Injection molding tonnage refers to the clamping force exerted by an injection molding machine to keep the mold closed during the injection molding process. It is a critical parameter in the injection molding industry and is measured in tons. The amount calculate injection molding tonnage required for a specific project depends on various factors.
What are common injection molding tonnage ranges?
The common injection molding tonnage ranges can vary depending on the specific requirements of the project, but here are some typical ranges:
Small Parts: Typically in the range of 5 to 100 tons. Examples include small plastic components, electronic parts, etc.
Medium Parts: Approximately in the range of 50 to 500 tons. Examples include components for household appliances, automotive interior parts, etc.
Large Parts: Around 200 to 2000 tons. Examples include automotive housings, large packaging containers, etc.

What are Key Considerations?
Product Size and Complexity:
Small and simple parts typically require lower tonnage, while larger and complex parts demand higher tonnage.
1. Small and Simple Parts:
For small and straightforward parts, opting for lower-tonnage machines is often more cost-effective and efficient. These machines handle lighter loads and simpler molds with ease.
Example: Small caps, fasteners, or basic components typically fall into this category.

2. Larger and Complex Parts:
Larger and more intricate parts demand higher tonnage to accommodate the increased material volume and intricacies of the mold. High-tonnage machines provide the necessary force to fill larger cavities and create detailed features.
Example: Automotive components, and intricate consumer goods.

3. Overall Size, Thickness, and Intricacy:
Evaluate the overall size, thickness, and intricacy of your product. Thicker and more complex parts may require additional force for proper material distribution and mold filling.
Example: Thin-walled electronic device housings vs. thick-walled structural components.

4. Material Characteristics:
Consider the characteristics of the material you are using. Some materials may require higher injection pressure, or longer injection times, impacting the tonnage requirements.
Example: High-performance engineering plastics vs. standard commodity plastics.
5. Mold Design Precision:
Precision in mold design is paramount. If your product involves intricate details or complex geometries, it may necessitate higher precision in the mold design, influencing the required part tonnage factor.
Example: High-precision medical devices or components with fine features.

Whether it’s a small and simple part or a larger, more complex component, understanding the factors outlined above is crucial for achieving optimal results in your injection molding process. If you have any questions or need further assistance, feel free to reach out. At Sino-Mold Industrial Co., Ltd., we are here to provide tailored solutions for your injection molding needs.
Material Characteristics:
Different materials have unique molding requirements.
1. High-Strength Materials:
Materials with high tensile strength or rigidity often necessitate higher injection molding tonnage. The increased force is required to effectively fill the mold with these sturdier materials, ensuring that the final product retains its structural integrity and meets the desired specifications.
2. High Flowability Materials:
Materials that exhibit high flowability, such as certain types of thermoplastics, may also require higher tonnage. This is because the molten material needs sufficient pressure to reach all parts of the mold, especially in intricate or detailed designs. Higher tonnage ensures that the material flows smoothly and uniformly into all areas of the mold, resulting in a well-formed final product.
For instance, if you are working with a high-strength polymer commonly used in engineering applications, the material’s resistance to flow may demand higher tonnage to fill the mold adequately. Conversely, a highly flowable material like some medical-grade plastics might still require higher tonnage to maintain precision in intricate features.
Clamping Force:
Ensure the clamping force is sufficient to hold the mold securely during injection.
1.Sufficient Clamping Force:
It is essential to ensure that the clamping force is sufficient for the specific mold being used. Inadequate clamping force can lead to several issues during the injection molding process.
2. Holding the Mold Securely:
The primary function of clamping force is to hold the mold securely closed during injection. This prevents any movement or separation of the mold halves, ensuring that molten plastic is contained within the mold cavity.
3. Preventing Flashing:
Insufficient clamping force can result in a phenomenon known as flashing. Flashing occurs when molten plastic escapes from the mold cavity and creates excess material along the parting line. Proper clamping force prevents this by keeping the mold tightly sealed, preventing any escape of material.
4. Completing Mold Filling:
Adequate clamping force is also crucial for complete mold filling. It ensures that the mold remains closed under the pressure of the injection, allowing the molten plastic to flow into all areas of the mold and form the desired product without voids or incomplete filling.
For example, if the clamping force is insufficient for a large and complex mold, there might be a risk of the mold opening slightly during injection, leading to flashing or incomplete filling. On the other hand, if the clamping force is excessively high for a smaller and less complex mold, it could result in unnecessary wear and tear on the equipment.
In summary, ensuring the clamping force is appropriately matched to the requirements of the mold is critical for the success of the injection molding process. It prevents defects, such as flashing, and ensures that the mold is securely closed for complete and accurate filling.
Melt Flow Rate:
The melt flow rate directly influences the tonnage requirements for injection molding machines. Different materials with varying MFRs may necessitate adjustments in tonnage to ensure optimal molding conditions.
1. High Melt Flow Rate:
Materials with a high melt flow rate, indicating good flowability, may require lower tonnage. These materials can efficiently fill the mold even at lower pressures, making them suitable for applications with lower clamping force.
2. Low Melt Flow Rate:
Conversely, materials with a lower melt flow rate, indicating lower flowability, may require higher tonnage. These materials may need additional pressure to fill the mold adequately, especially for parts with intricate details or thicker sections.
3. Ensuring Optimal Flow:
Optimal flow is crucial for achieving precise molding without defects. Matching the full tonnage of an injection to the melt flow rate ensures that the molten plastic can flow uniformly into all areas of the mold, preventing issues such as incomplete filling, voids, or uneven distribution of material.
Example:
For instance, a material with a high melt flow rate, like some polyethylenes, might be suitable for low-tonnage applications where fast and efficient filling of the mold is required. In contrast, a material with a lower melt flow rate, such as some engineering plastics, might require higher tonnage to achieve the necessary pressure for complete mold filling.
Part ejection is a critical phase in the injection molding process where the formed product is removed from the most suitable injection molding machine. The force required for this operation is an essential consideration in determining the appropriate tonnage for the injection molding machine.
Part Ejection:
1. Influence on Tonnage Requirements:
Insufficient tonnage can pose challenges during the ejection process. If the clamping force is not adequately matched to the requirements of part ejection, it may result in difficulties or complications when removing the molded part from the mold.
2. Factors Affecting Ejection Force:
Several factors influence the force needed for part ejection, including the design complexity of the part, the surface finish of the mold, and the type of ejection system employed. A well-designed mold and an appropriately calculated ejection force are essential for smooth and efficient part removal.
3. Consequences of Inadequate Tonnage:
Consequences of Inadequate Tonnage:
Insufficient tonnage can lead to issues such as:
Incomplete Ejection: The molded part may not be fully ejected from the mold, resulting in incomplete demolding.
Part Deformation: Inadequate force may cause the part to deform during ejection, affecting its dimensional accuracy and surface finish.
Increased Cycle Time: Difficulties in part ejection can prolong the overall molding cycle time, reducing production efficiency.
Example:
In conclusion, considering the force required for part ejection is integral to determining the suitable tonnage for injection molding. Matching the tonnage to the ejection force requirements ensures a seamless demolding process, contributing to the overall quality and efficiency of the injection molding operation.
Machine Type:
Different injection molding machines have varying tonnage capacities.
1. Considerations for Machine Type:
Tonnage Range: Injection molding machines are available in a wide range of tonnages, from small to large. The tonnage required for your project depends on factors like the size, complexity, and material characteristics of your molded part. Ensure that the machine’s tonnage range encompasses the requirements of your specific project.
Machine Specifications: Each injection machine model has unique specifications, including its clamping force, injection capacity, and mold dimensions it can accommodate. Carefully review the technical specifications of different machines to find one that suits the needs of your injection molding project.
2. Influence on Project Success:
The tonnage capacity of the machine directly influences the quality and consistency of the molded parts. Selecting a machine with insufficient tonnage may lead to issues such as incomplete mold filling, flashing, or difficulties in part ejection. Conversely, a machine with excessive tonnage may result in over-packing, leading to increased material stress and potential defects in the final product.
3. Matching Tonnage to Project Requirements:
Ensure that the chosen injection molding machine’s tonnage aligns precisely with the requirements of your project. This involves considering the size and complexity of the parts, as well as the characteristics of the chosen material. A well-matched machine ensures optimal performance, efficiency, and part quality throughout the production cycle.
Example:
For example, if your project involves the production of small and intricate components, opting for a machine with lower tonnage may be suitable. On the other hand, larger and more complex parts may necessitate a machine with higher tonnage to accommodate the increased clamping force requirements.
Tolerance and Quality:
Maintain a balance between tonnage and precision to achieve the desired part quality.
Avoid excess tonnage that might lead to over-packing and part distortion.
Why Choose Sino-Mold Industrial Co., Ltd.?
At Sino-Mold, we understand the nuances of injection molding. Our state-of-the-art facilities and experienced team ensure precise tonnage selection tailored to your project’s unique needs. With a commitment to quality and efficiency, we’ve become a trusted partner for clients worldwide.
Conclusion:
Choosing the right injection molding tonnage is a crucial step in ensuring the success of your project. At Sino-Mold Industrial Co., Ltd., we specialize in providing comprehensive injection moldmaking and molding solutions. Contact us at louise@sino-mold.com for personalized assistance or to discuss your project requirements.